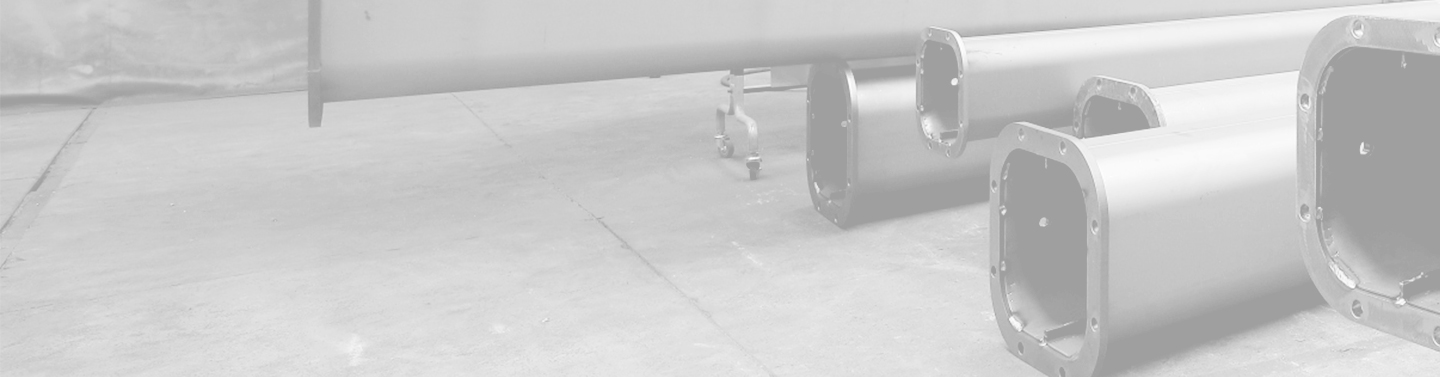
Leonardo Product Configurator
Leonardo Product configura velocemente paranchi a catena, paranchi fune e gru a bandiera da soli o in combinazione; permette di configurare tutti i tipi di paranco standard e gru a bandiera in trave standard a rotazione sia manuale ed elettrica, con e senza paranco, nelle diverse possibili versioni e opzioni.
Nella sua versione completa offre inoltre la possibilità di scaricare direttamente i disegni della propria configurazione sia in formato 2D che 3D e di ricevere l’offerta in tempo reale.
Possiedi già un account come RIVENDITORE? Clicca qui per accedere alla VERSIONE COMPLETA del configuratore:
Sei un rivenditore e desideri ottenere le credenziali di accesso? Contattaci.
Leonardo Crane Set Configurator
Configura ponti appoggiati in combinazione con relativi paranchi
Leonardo CraneSet Configurator, permette di configurare strutture a ponte complete di testate, carrelli e paranchi a seconda delle esigenze dimensionali e di portate. Grazie alla forte versatilità aiuta in fase di progettazione a soddisfare le necessità del cliente e fornire un preventivo dettagliato comprensivo di tutti i componenti e accessori. Il configuratore Leonardo CraneSet, è inoltre in grado di fornire al cliente le informazioni necessarie ai dimensionamenti strutturali.